How Do I Minimize Push-Back From the Assembler Regarding My BOM?
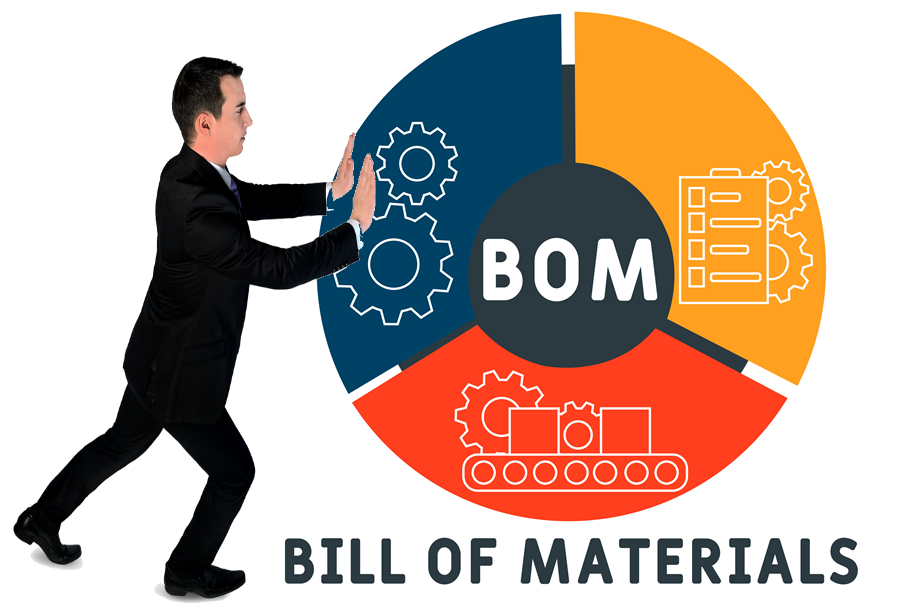
Today we will review what you can do to ensure there are no questions from the Assembler with a brief list of what things are necessary for a Bill of Materials (BOM).
PCB:
Let's talk about the PCB, which is an integral part of the BOM. So many customers omit the PCB from the BOM. There is an assumption that parts contained in the BOM go on the PCB, so they frequently forget to add it.
Note: the PCB should have a P/N and revision.
Quantities:
Next to review is "Quantities of parts." Quantities must match the Reference designators called out. If parts have been added due to a PCB change, make sure the Quantity reflects ALL the changes.
Example:
Calling out a QTY of 1 but listing five of the same MFG P/N means the part count will be off. This would have to be caught and clarified in either the BOM audit, the KIT review, or the Assembly Documentation. No need to remind you that a customer clarification takes time.
DNP/DNI:
I did an Audit sheet recently that had multiple locations for DNI/DNP.
Example:
In one case, the text "DNI/DNP" was not present for the MFG P/N, but the part QTY was zero. (Indicating it should not be populated)
On the following line, the text DNI/DNP was in a column on the far right-hand side of the BOM, and in the following line, the DNI/DNP was in a line after the reference designators.
I recommend placing all DNI/DNP information in the same place in the documents. This helps eliminate confusion, and the person creating the Audit sheet may miss a DNP/DNI.
I have seen BOMs where ALL DNI/DNP parts are grouped, making it quite simple for the BOM auditor. I do NOT recommend you leave the REF DES (Reference designators) with the parts AND list them separately, describing ALL DNI/DNP's. (Choose One method.)
IMPORTANT:
If one out of four parts is to be DNP/DNI (Do Not Populate/ Do Not Install), consider removing the DNP/DNI from the line with three others that ARE populated to avoid confusion and have a part that you did not intend to be on the PCB.
Reference Designators (REF DES):
Now I want to focus a bit on the Reference Designators.
Making one protracted line with no commas or spaces between Reference designators will have the assembly software thinking it is one long part name. Make sure you separate Reference designators by a comma or a space.
TIPS:
- If there are multiple parts of the same MFG P/N in sequence, you can record the multiple parts with something similar to "U21-28".
- Do NOT use dash numbers in the Reference designators.
Example of what NOT to do: "U1-1, U1-2,".
I recommend using an underscore and calling them "U1_1, U1_2."
During an audit, I found the customer alternated between using commas and periods. This results in Quantity issues during the Audit. Replacing the 'periods' with 'commas' and the Quantity was then correct.
Part descriptions:
I understand the engineer may want to separate these into different columns.
- One column for footprint size
- One column for Power numbers
- One column for a part description in terms of how many rows an IC may be, etc.
The problem with this scenario is:
When the person doing the BOM audit gets the job, all that information needs to be in one column. If the part descriptions are separated into different columns, the BOM audit person may have to Concatenate (combine) them into ONE description. Additionally, some engineers want a FULL description that may be more than an assembly machine can handle.
For instance:
"Polymeric PTC Resettable Fuse 33V 1.85A Ih Surface Mount 2920 (7351 Metric), Concave"
This description can easily be reduced to:
"FUSE, 33V 1.85A, 2920"
In this case, all the critical info is there.
"FUSE" is the type of component
"33V 1.85A" is the Power
"2920" is the footprint size
EXAMPLE:
If the parts are run on a JUKI machine, the description must be 127 characters or LESS and should NOT contain any special characters.
It has been my experience that the short descriptions on Digi-Key or Mouser or almost any part distributor is better than the long ones for the assembly machines. The shorter descriptions provide all necessary information about the component from a kit audit standpoint. It also saves time to query all the MFG part #'s in Digi-Key to get a shorter description. (Especially on the bigger BOMs)
The opposite is also true. Simply calling out a Capacitor of a specific size and threshold simply as "CAP," with no additional information, means the KIT auditor cannot truly verify the part as far as Footprint size or Power threshold.
Again, keep the part descriptions to a minimum but contain all the info necessary to validate the part at the KIT audit.
Remember that when the EQ (Engineering Questions) are sent to the customer, it is effectively "ON HOLD" awaiting a response. A prompt response will mean no time loss.
MFG P/N's:
Manufacturing part numbers (or Customer part numbers) are needed to purchase parts if the job is a turn-key and validate the parts if consigned.
If you provide a Vendor Part Number (VPN) and a Manufacturing Part Number, please do not "blend" the information by entering some in the Vendor Part Number column and some in the Manufacturing Part Number column and vice versa.
I have seen BOMs where the customer mixed MFG P/Ns, vendor numbers, and alternate parts on top and below the primary part number. This takes extra time to fix the audit sheet before passing it on to the KIT check.
Note: If using ONLY Customer P/Ns, the job must be consigned. For us to order the parts (Consigned or a mix of Turnkey and Consigned), we would need the Manufacturer's Part Number.
What's missing:
ALL columns should be COMPLETE. Missing quantities, missing REF DES, or missing MFG P/Ns or Customer Part Numbers require the sales engineer for the Assembler to backtrack and ask the customer for the missing information. This does not take much time, but the risk of losing a single day for a three-day turn time is immense.
Alternates:
We all know part shortages are real and frequently happen when a job is consigned or partially consigned. Having a plethora of alternate parts is a wonderful way of ensuring the assembly will not go on hold for part shortages.
But adding 5 to 10 times the amount of alternate parts and NOT having a part description takes additional time when going to Digi-key, Mouser, or another part supplier at the audit stage. This requires more time to get a description for the alternate and validate the parts at the BOM audit stage.
The alternates SHOULD be the same footprint size (0201 as an example) and value (10uf as an example). But the alternates may have a different power threshold like 10V vs. 50V. This is where the BOM auditor may require clarification, which takes additional time.
Also, I frequently see alternates that are obsolete parts. Taking a little time to research the alternates you choose ensures they can still be procured.
In summary, here is a brief list of what things are necessary for a BOM:
- PCB - Include the part number and rev.
- A Part QUANTITY for each MFG P/N.
- Note the parts NOT to be populated on the PCB. There are many ways to stipulate this, can be DNI (Do Not Install) or DNP (Do Not Populate) or even "NO STUFF" or "NOT FITTED."
- Reference Designators - Must be the same as on the Gerber Silkscreen for the PCB. Also, add dots for polarity for I/C's and any other part that requires a polarity and either "A" for Anode, "K" for Cathode, or a line with a description of whether the line represents Cathode or Anode for all Diodes (Unless Bi-directional)
- A Brief part description with the main things needed to verify the parts. Type of component, Power, and Footprint size.
- Part Numbers- either MFG Part Numbers (if turn-key) or a Customer Part Number (if consigned) or both. Vendor and Vendor part numbers are helpful but not necessary.
- Any Alternate parts that can be used in case the primary part number cannot be obtained.
That's all for now.
As always, Thanks for reading!
(If you are interested in other loss-of-time solutions, be sure to check out
"Avoiding Time Loss Due to EQs From the Fabricator.”)
About the Author
Mark Thompson C.I.D. - Sr. PCB technologist/ Engineering Manager
Mark has been in the engineering field for over 38 years. In 1993, he relocated to the Pacific Northwest, where he worked for Pacific Circuits, which became TTM, and Praegitzer Industries. He worked with Prototron from 1996–2019 and is now an engineering manager at Out of the Box Manufacturing.
He is passionate about his career, followed by aviation, art, and history. In his free time, Mark is an avid pilot, with a fondness for the aircraft of yesteryear. Mark says, "I have been privileged to fly many biplanes from the 1930s and 1940s, including Fleets, Stearmans, and N3Ns."
Mark enjoys sharing information and answering questions about PCB fabrication. Mark says: “The more information I can provide, the more fulfilled my customers and I will be.” Reach out to Mark here.